|
|
|
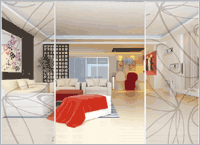 |
INO ink is denaturalized acrylic resin ink, which has strong adhesion to glass and metal under low-temperature or air dry (24 hours). This ink forms the cohesion structure by the second reaction rather than that of the first reaction, and it is the two-component ink with overall better qualities. This has good adhesion for mineral materials (glass, ceramics, pottery, metals). High-temperature treatment (500°C~600°C) is essential for glass, but this hardener-used ink only requires the minimum 150°C treatment for eight minutes or air drying with relatively good qualities. The use of spray thinner makes the spray painting possible.
|
|
|
Main features |
|
ITEM |
CONTENTS |
Ink type
|
Baking or air dry type denaturalized Acrylic Resin
|
Applicable materials
|
Glass, ceramic, crystal, aluminum, stainless steel
|
Gloss |
Glossy (control able to semi-gloss, non gloss by matte agent) |
Drying time |
Heat drying 150°C 15~20 min. Air dry (24~48 hours)
|
Thinner
|
Standard solvent: methyl salicylate, low oder thinner Spray thinner: Standard, wintertime type
|
Coverage Area and Packing
|
Printing area 30~40 m²/kg Kg, 4kg (G/A), 17kg (steel, plastic)
|
|
|
|
|
Characteristics |
- Appearance: viscous fluid - Solidity: 45~70% - Viscosity: 23.000~29.000 cPs (at 25°C) - Flash point: 42~46°C - Boiling point: 165~220°C |
|
|
Mixing Ratio of Hardener |
|
• Used hardener: INO hardener • Mixing ratio: INK : Hardener = 100:3 Medium, 4 Color →INK : Hardener= 100:4 • Mix hardener with ink, fully then use it after 10 minutes. The ink with hardener mixed becomes hardened after 7~8 hours, so it needs to be mixed as the amount used to save cost. • It takes 2~3 hours for drying of touch, and takes hardening hours(about 24 hours) for complete drying, so avoid the contact loading of printing materials within 24 hours. • Adhesion test is required after 24 hours, the more time passes (2~3 days), the stronger the adhesive strength becomes. • The rest of hardener must be used within a month, and the hardener is sealed tightly not to contact with air. |
|
|
Ink film test results |
|
Item
|
Test Method
|
Result
|
1. Adhesion
|
100/100 Cross cut (1mm)
|
100/100
|
2. Hardness
|
Pencil hardness 45° x 500g
|
3H
|
3. Solvent resistance
|
MEK, Toluene, methanol, gasoline, soaking for 24 hours
|
Not affected
|
4. Chemical resistance |
5% H₂SO₄/24 hrs
|
Not affected
|
5% Na₂CO₃/24 hrs
|
5. Moisture resistance
|
50±2°C, 98±2% Rh/ 10 days
|
Not affected
|
6. Cold-Heat resistance
|
Cycle (-40°C x 2hrs ↔ 80°C x 90%Rh x 2hrs) 10 times
|
Not affected
|
Test condition (1 day after printing) Material: glass Drying: 150°C, 10min. |
|
|
|
Color guide (High Grade color) |
|
|
105 White
|
625 Pink
|
4 color P245 Process Yellow
|
135 Opaque white
|
335 Mid green
|
P445 Process Cyan
|
215 Lemon yellow
|
355 Fast green
|
P545 Process Magenta
|
235 Mid yellow
|
435 Mid blue
|
P745 Process Black
|
255 Deep yellow
|
455 Deep blue
|
Special color
|
515 Orange
|
465 Royal blue
|
Various silver, gold
|
535 Bright red
|
655 Violet
|
Various pearl (red, gold, white)
|
555 Deep red
|
715 B. black
|
Phosphorescent, sparkling
|
575 Mid red
|
735 Opaque black
|
Pantone mixing color
|
615 Magenta
|
805 Medium
|
Coating medium
|
|
|
- For the degree of color intensity, mix and control it with 805 Medium. - In case that the end digit (●) of color number (○○●) digits is 2 or 3, it may cause change of color when it is used in outdoors for a long time. In case of 4 or 5, it can be used in outdoors for three years of more. - In case of air bubbles during printing, mix 1~2g defoamers evenly and use it. - Color range: Standard color 20 colors High grade color 20 colors
|
|
|
Safety and Non-toxicity |
|
• It does not contain toxic substances such as carcinogen and heavy metal. • It does not contain heavy metal components such as Lead, Cadmium by the overseas standard. RoHS - Cd, Pb, Hg, Cr6+, PBBs, PBDEs • It has high natural ignition point, so it is safe if it is not intentional incendiarism. |
|
|
Caution |
• Fully stir up the contents prior to use that they can be mixed well. • Do not mix it with other kinds of ink. • It may not be fit with some materials, so use it after sufficiently looking it over. • Use a designated diluent by all means. • For products requiring light-resistance and heat resistance. Inquire them into the purchase shop. • Handle it at well-ventilated place, and keep it with its lid well closed at a designated place. • Keep out of reach of children. It is harmful by inhalation, in contact with skin and if swallowed. • Take notice of flames heats, and keep away from them. • For other inquiries, ask them to the purchase shop. “MSDS” is available on request. |
|
|
|
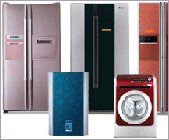 |
GLSA Ink is one-component, baking type denaturalized acrylic ink. Originally, ceramic ink is ideal for glass ink treated under 500~600 ° C, but this ink has cost efficiency and equivalent adhesion, water resistance, and solvent resistance as well. The use of advanced pigments and non-discoloration resin prevents discoloration on materials outside for three to five years. GLSA ink is glass ink, widely used for architectures, interior, mobile phones, furniture, lightings, and electronics. The use of spray thinner makes the spray painting possible. (GLSA coat) |
|
|
Main features |
|
ITEM |
CONTENTS |
Ink type
|
Baking type denaturalized Acrylic Resin
|
Applicable materials
|
Glass, ceramic, crystal, aluminum, stainless steel
|
Gloss
|
Glossy (control able to semi-gloss, non gloss by matte agent)
|
Drying time |
Heat drying 180°C, 10~30 min. |
Thinner |
Standard solvent: DBE, Methyl salicylate, low oder thinner Spray thinner: Standard, Wintertime type
|
Coverage Area and Packing
|
Printing area 30~40 m²/kg Kg, 4kg (G/A), 17kg (steel, plastic)
|
|
|
|
Specifications of Ink |
- Appearance: viscous fluid - Solidity: 45~70% - Viscosity: 30,000~40,000 cPs (at 25°C) - Flash point: 42~46°C - Boiling point: 165~220°C |
|
|
Ink film test results |
|
Item
|
Test Method
|
Result
|
1. Adhesion
|
100/100 Cross cut (1mm)
|
100/100
|
2. Hardness
|
Pencil hardness 45° x 500g
|
3H
|
3. Solvent resistance
|
MEK, Toluene, methanol, gasoline, soaking for one week
|
Not affected
|
4. Boiling resistance
|
98±2°C/ 30 min., 30 min after cross cutting
|
100/100
|
5. Chemical resistance
|
5% H₂ SO₄ /24 hrs,
|
Not affected
|
5% Na₂ CO₃/24 hrs
|
6. Moisture resistance
|
50±2°C, 98±2%Rh/ 10 days
|
Not affected
|
7. Cold-Heat resistance
|
Cycle (-40°C x 2hrs ↔ 80°C x 90%Rh x 2hrs) 10 times
|
Not affected
|
8. Heat resistance
|
200±5°C/1 hour
|
Not affected
|
9. Saltwater resistance
|
35°C, 5%NaCl/ 360 hrs. less than 1/16˝
|
Not affected
|
10. Ultraviolet resistance
|
After 24 hrs test, it should be less than △E=3.0 (15W x 20cm)
|
Not affected
|
11. Water resistance
|
Soaking for 1 month
|
Not affected
|
|
|
Test condition (1 day after printing) Material: glass Drying: 180°C 10min.
|
|
|
|
Color guide(High grade color) |
|
105 White
|
625 Pink
|
4 color P245 Process Yellow
|
135 Opaque white
|
335 Mid green
|
P445 Process Cyan
|
215 Lemon yellow
|
355 Fast green
|
P545 Process Magenta
|
235 Mid yellow
|
435 Mid blue
|
P745 Process Black
|
255 Deep yellow
|
455 Deep blue
|
Special color
|
515 Orange
|
465 Royal blue
|
Various silver, gold
|
535 Bright red
|
655 Violet
|
Various pearl (red, gold, white)
|
555 Deep red
|
715 B. black
|
Phosphorescent, sparkling
|
575 Mid red
|
735 Opaque black
|
Pantone mixing color
|
615 Magenta
|
805 Medium
|
Coating medium
|
|
|
- For the degree of color intensity, mix and control it with 805 Medium. - In case that the end digit (●) of color number (○○●) digits is 2 or 3, it may cause change of color when it is used in outdoors for a long time. In case of 4 or 5, it can be used in outdoors for three years of more. - In case of air bubbles during printing, mix 1~2g defoamers evenly and use it. - Color range: Standard color 20 colors High grade color 20 colors
|
|
|
Safety and Non-toxicity |
• It does not contain toxic substances such as carcinogen and heavy metal. • It does not contain heavy metal components such as Lead, Cadmium by the overseas standard. RoHS - Cd, Pb, Hg, Cr6+, PBBs, PBDEs • It has high natural ignition point, so it is safe if it is not intentional incendiarism. |
|
Caution |
• Fully stir up the contents prior to use that they can be mixed well. • Do not mix it with other kinds of ink. • It may not be fit with some materials, so use it after sufficiently looking it over. • Use a designated diluent by all means. • For products requiring light-resistance and heat resistance. Inquire them into the purchase shop. • Handle it at well-ventilated place, and keep it with its lid well closed at a designated place. • Keep out of reach of children. It is harmful by inhalation, in contact with skin and if swallowed. • Take notice of flames heats, and keep away from them. • For other inquiries, ask them to the purchase shop. “MSDS” is available on request. |
|
|
|
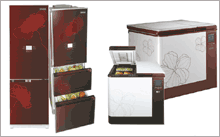 |
GL-1 ink is a thermosetting modified acrylic ink, whose adhesion on glass is improved by acrylic and special resin. Originally the ideal type of glass ink is a high temperature-treated (500~600℃) ceramic ink. However, GL-1 ink is cheaper than that, having adhesion, water resistance and solvent resistance similar to that. Use of high grade pigments and non-yellowing resin allow no discoloration when being left outdoors for a long time (3~5 years). GL-1ink is dedicated for glass, widely used for building, interior, furniture, lamps, and electronic products. Using a thinner for spray makes possible spray painting.
|
|
|
◈ Major features |
|
ITEM
|
CONTENTS
|
Ink type
|
Thermosetting modified acrylic compound, non-yellowing resin ink |
Material applicable |
Glass |
Gloss |
Semi-dull (Matte adjustable by dulling agent) |
Drying conditions |
Hot air drying (180℃, 20 min.), IR drying (180℃, 10 min.) |
Thinning solvent |
Standard solvent (retardant solvent): Cyclohexanone, methyl salicylate, non-toxic, non-smell retardant, thinner for spray (general type, quick dry type) |
Printable area and packing unit |
30~40㎡/kg, kg, 4kg(GA), 17kg (plastic, steel can)
|
|
|
|
◈ Ink properties |
|
o. Appearance : Viscous liquid o. Solid content : 40 ~ 70% o. Viscosity : 12,000 ~ 14,000cPs. (at 25℃) o. Specific gravity : 0.900-1.500 o. Flash point : 42 ~ 46℃ o. Boiling point : 165 ~ 220℃
|
|
|
◈ Physical properities |
|
TEST ITEM
|
TEST METHOD
|
DECISION
|
Adhesion
|
100/100 CROSS CUT (1mm distance) |
100/100 |
Hardness
|
Pencil hardness 45° x 500g |
Over 2H |
Solvent resistance
|
MEK, Toluene, Methanol, Gasoline/ 1Deposit for 1 week |
No effect
|
Boiling water resistance |
98±2℃, Deposit for 60 min., Cross cutting after 30 min. |
100/100 |
Chemical resistance |
5% H2SO4 / 24Hrs |
No effect |
5% Na2CO3 / 24Hrs |
No effect |
Humidity resistance
|
50±2℃, 98±2%RH, 10 Days |
No effect |
Cold/heat resistance
|
CYCLE(-40℃×2Hrs ↔ 80℃×90%RH×2Hrs) 10회 |
No effect |
Heat resistance
|
200±5℃ / 1Hrs |
No effect |
Chlorine spray resistance |
35℃, 5%NaCl / 360Hrs |
No effect |
UV resistance
|
After irradiation for 24Hrs, △E=below 3.0 (15Wx20cm) |
No effect |
Water resistance
|
Deposit for 1 month. |
No effect |
Silicon coating
|
Silicone coating for 24Hrs, irradiation for 360Hrs |
No effect |
Urethane foaming
|
BASF urethane foam liquid for 24Hrs, irradiation for 260Hrs |
No effect |
※The above physical property test was done one day after printing on the glass plate and drying (at 180℃, 10 min.) |
|
|
|
◈ Color range |
|
1) High grade color: 16 colors (Use of Class 5 high grade pigments, weatherability for 3~5 years) |
105 White |
625 Pink |
4 color P245 Process Yellow |
215 Lemon yellow |
335 Mid green |
P445 Process Cyan |
235 Mid yellow |
355 Fast green |
P545 Process Magenta |
255 Deep yellow |
435 Mid blue |
P745 Process Black |
515 Orange |
455 Deep blue |
Special color |
535 Bright red |
655 Violet |
Various silver, gold |
555 Deep red |
726 B. black |
Various pearl (red, gold, white) |
575 Mid red |
805 Medium |
Phosphorescent, sparkling |
615 Magenta |
Multi 800C Medium |
Pantone mixing color |
|
|
|
1. Concentration is adjusted by 805 transparent ink.2. If Third digit of identification number (Arab numerals) of each color ( ○○● ) is 2~3, if exposed outdoors for 0.6~2 years, the color may disappear; and if 4~5, if high grade proven pigments are used, no discoloration is possible for 3~5 years. 3. If bubbles occur while printing and 1~2g antifoaming agent is mixed, they will disappear. |
|
|
◈ Safety and non-toxicity |
|
ㅇHeavy metals and other harmful substances are not contained. ㅇHeavy metal components like lead or cadmium according to foreign toy inspection standards are not contained. RoHS( Cd, Pb, Hg, Cr6+, PBBs, PBDEs) ㅇIts high ignition point keeps safe from fire without intentional fires. |
|
|
◈ Instructions for use |
|
ㅇStir sufficiently so that the content is well mixed before use ㅇDo not blend with other kinds of ink. ㅇAs this may not be suitable for a certain material, examine thoroughly before use. ㅇIf possible, use a designated thinner. ㅇFor products requiring light stability and heat resistance, be sure to ask our distributor. ㅇHandle in a well ventilated area. After use, close the cap completely and store in a designated place. ㅇKeep out of reach of children. ㅇUse caution with fire. Keep away from fire. ㅇFor other inquiries, please ask our distributor. Please refer to "MSDS".
|
|
|
|
|
|
|
GL-2 ink is a modified acrylic resin ink; two-component ink whose adhesion and physical properties are most excellent among glass ink (GLSA, INO). With the use of curing agent, its solvent resistance, silicon resistance, water resistance and cold/heat resistance are excellent. Using high grade pigments and non-yellowing resin, if left outdoor for a long time (3~5 years), it will not be discolored It is widely used for refrigerators, air conditioners, home appliances, mobile phones and interior lamps. In case of overprinting, curing temperature of prime printing should be low. Overheated curing for overprinting may cause a problem with ink interlaminar adhesion. After complete curing film performances are very excellent and of superior physical properties.
|
|
|
◈ Major features |
|
ITEM
|
CONTENTS
|
Ink type
|
Modified acrylic compound, non-yellowing resin ink |
Material applicable |
Glass |
Gloss |
Semi-dull (Matte adjustable by dulling agent) |
Drying conditions |
Hot air drying (180℃, 20 min.), IR drying (170~180℃, 10 min.) |
Curing agent |
HG-200 curing agent (Non-yellowing type) |
Thinning solvent |
Standard solvent (retardant solvent): Cyclohexanone, methyl salicylate, non-toxic, non-smell retardant, thinner for spray (general type, quick dry type) |
Printable area and packing unit |
30~40㎡/kg, kg, 4kg(GA), 17kg (plastic, steel can)
|
|
|
|
[Curing agent HG-200]
|
105 White- ink : curing agent = 8 : 1, 725 Black- ink : curing agent = 7 : 1, 805 Transparent- ink : curing agent = 5 : 1 |
o. Standard ink lifetime mixed with curing agent is 12 hours at room temperature. It this time passes, ink becomes self-curing and only the quantity designated for mixing shouold be used. As curing time is affected by temperature, it may be shorter in summer (high temperature) than standard time, while it may be later in winter (low temperature). o. Be sure to do adhesive test after 24 hours. As time passes (2~3 days), adhesion becomes stronger. o. Close the cap tightly for the remaining curing agent and minimize the contact with air.
|
|
◈ Ink properties |
|
o. Appearance : Viscous liquid o. Solid content : 40 ~ 70% o. Viscosity : 12,000 ~ 14,000cPs. (at 25℃) o. Specific gravity : 0.900~1.500 o. Flash point : 42 ~ 46℃ o. Boiling point : 165 ~ 220℃
|
|
|
◈ Physical properities |
|
TEST ITEM
|
TEST METHOD
|
DECISION
|
Adhesion
|
100/100 CROSS CUT (1mm distance) |
100/100 |
Hardness
|
Pencil hardness 45° x 500g |
Over 2H |
Solvent resistance
|
MEK, Toluene, Methanol, Gasoline/ 1Deposit for 1 week |
No effect
|
Boiling water resistance |
98±2℃, Deposit for 60 min., Cross cutting after 30 min. |
100/100 |
Chemical resistance |
5% H2SO4 / 24Hrs |
No effect |
5% Na2CO3 / 24Hrs |
No effect |
Humidity resistance
|
50±2℃, 98±2%RH, 10 Days |
No effect |
Cold/heat resistance
|
CYCLE(-40℃×2Hrs ↔ 80℃×90%RH×2Hrs) 10회 |
No effect |
Heat resistance
|
200±5℃ / 1Hrs |
No effect |
Chlorine spray resistance |
35℃, 5%NaCl / 360Hrs |
No effect |
UV resistance
|
After irradiation for 24Hrs, △E=below 3.0 (15Wx20cm) |
No effect |
Water resistance
|
Deposit for 1 month. |
No effect |
Silicon coating
|
Silicone coating for 24Hrs, irradiation for 360Hrs |
No effect |
Urethane foaming
|
BASF urethane foam liquid for 24Hrs, irradiation for 260Hrs |
No effect |
※The above physical property test was done one day after printing on the glass plate and drying (at 180℃, 10 min.) |
|
|
◈ Color range |
|
1) High grade color: 16 colors (Use of Class 5 high grade pigments, weatherability for 3~5 years) |
INK
|
COLOR MIX (MICRO PARTICLE ㎛)
|
COLOR MIX (NANO PARTICLE ㎚)
|
105 White |
H-YELLOW |
S-YELLOR |
726 B. black |
L-YELLOW |
S-RED |
805 Medium |
RED |
S-BLUE |
805(P) Medium |
BLUE |
S-VIOLET |
|
VIOLET |
S-BLACK |
|
BLACK |
|
|
|
|
1. Concentration is adjusted by 805 transparent ink.2. If Third digit of identification number (Arab numerals) of each color ( ○○● ) is 2~3, if exposed outdoors for 0.6~2 years, the color may disappear; and if 4~5, if high grade proven pigments are used, no discoloration is possible for 3~5 years. 3. If bubbles occur while printing and 1~2g antifoaming agent is mixed, they will disappear. |
|
|
◈ Safety and non-toxicity |
|
ㅇHeavy metals and other harmful substances are not contained. ㅇHeavy metal components like lead or cadmium according to foreign toy inspection standards are not contained. RoHS( Cd, Pb, Hg, Cr6+, PBBs, PBDEs) ㅇIts high ignition point keeps safe from fire without intentional fires. |
|
|
◈ Instructions for use |
|
ㅇStir sufficiently so that the content is well mixed before use ㅇDo not blend with other kinds of ink. ㅇAs this may not be suitable for a certain material, examine thoroughly before use. ㅇIf possible, use a designated thinner. ㅇFor products requiring light stability and heat resistance, be sure to ask our distributor. ㅇHandle in a well ventilated area. After use, close the cap completely and store in a designated place. ㅇKeep out of reach of children. ㅇUse caution with fire. Keep away from fire. ㅇFor other inquiries, please ask our distributor. Please refer to "MSDS".
|
|
|
|
|
|
|
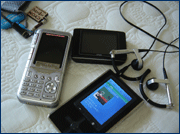 |
MIRROR INK SERIES are heat-and-dry type ink, using special synthetic resin and special metallic silver, and they generate an effect similar to mirrors on glass and plastic materials. Special metallic flavors can also be generated. The alternative effect for hot stamping is also feasible. For glass, Mirror-600 and G-Mirror are available. For plastics(acrylic, PC, PET), Mirror-1000 and P-Mirror are available.
|
|
|
Main features |
|
ITEM |
CONTENTS |
Ink type
|
Heat and dry type with special synthetic resin
|
Applicable materials
|
For glass : Mirror-600, G-Mirror For plastics(Acrylic, PC, PET) : Mirror-1000, P-Mirror
|
Gloss
|
High glossy, mirror effect
|
Drying time |
Mirror-600, G-Mirror : 150 ℃, for 10 minutes or 180℃ for 8 minutes Mirror-1000, P-Mirror : natural dry for 24 hours or 60℃ for 30 minutes
|
Thinner |
BC(Butyl Cellosolve)
|
Coverage Area and Packing
|
30~40 m²/kg kg, 4kg(GA), 17kg(plastic, steel can)
|
|
|
|
Specifications of Ink |
|
o. Appearance: Low viscous fluid o. Solid: 10% o. Viscosity: 500~1,000 cPs (at 25℃) o. Specific Gravity: 0.95~1.00 o. Flash point: 42~46℃ o. Boiling point: 165~220℃ |
|
|
Mixing Ratio of Hardener ( mirror 800 for glass) |
|
• Used hardener: K-hardener • Mixing ratio - INK: Hardener = 100: 3~7% • Mix hardener with ink, fully then use it after 10 minutes. The ink with hardener mixed becomes hardened after 7~8 hours, so it needs to be mixed as the amount used to save cost. • It takes 2~3 hours for drying of touch, and takes hardening hours(about 24 hours) for complete drying, so avoid the contact loading of printing materials within 24 hours. • Adhesion test is required after 24 hours, the more time passes (2~3 days), the stronger the adhesive strength becomes. • The rest of hardener must be used within a month and the hardener is sealed tightly not to contact with air. |
|
|
Ink film test results |
|
Item |
Test Method |
Result |
Adhesion |
100/100 Cross cut (1mm)
|
100/100
|
Hardness |
Pencil hardness 45° x 500g
|
3H
|
Moisture resistance |
50±2°C, 98±2%Rh/ 10 days
|
Not affected
|
Cold-Heat resistance |
Cycle (-40°C x 2hrs ↔ 80°C x 90%Rh x 2hrs) 10 times
|
Not affected
|
Heat resistance |
200±5°C/1 hour
|
Not affected
|
Ultraviolet resistance |
After 24 hrs test, it should be less than △E=3.0 (15W x 20cm)
|
Not affected
|
|
Test condition (1 day after printing) Material: glass, PC Drying: 180°C 10min. (Glass), 60°C 10min. (Plastic)
|
|
|
Safety and Non-toxicity |
|
• It does not contain toxic substances such as carcinogen and heavy metal. • It does not contain heavy metal components such as Lead, Cadmium by the overseas standard. RoHS - Cd, Pb, Hg, Cr6+, PBBs, PBDEs • It has high natural ignition point, so it is safe if it is not intentional incendiarism. |
|
Caution |
|
• Fully stir up the contents prior to use that they can be mixed well. • Do not mix it with other kinds of ink. • It may not be fit with some materials, so use it after sufficiently looking it over. • Use a designated diluent by all means. • For products requiring light-resistance and heat resistance. Inquire them into the purchase shop. • Handle it at well-ventilated place, and keep it with its lid well closed at a designated place. • Keep out of reach of children. It is harmful by inhalation, in contact with skin and if swallowed. • Take notice of flames heats, and keep away from them. • For other inquiries, ask them to the purchase shop. “MSDS” is available on request. |
|
|
|
|
|