|
|
PP Ink is economical and practical ink. SG#4000 series ink is screen ink for polypropylene materials manufactured by mixing and distributing high-class pigments. It uses excellent acrylic and chlorine rubber synthetic resin and is especially fit for materials that are difficult to attach, such as untreated Polypropylene or polyethylene terephthalate.
|
|
Main features |
|
ITEM |
CONTENTS |
Ink type
|
Air-drying, Polypropylene resin
|
Applicable materials
|
PP, untreated PP, PET
|
Gloss
|
High glossy (controllable to semi-gloss, non-gloss by matte agent)
|
Drying time
|
Air drying 5~20 min / heat drying 1~5 min at 60℃
|
|
|
|
pecifications of Ink |
o. Appearance: Viscous fluid o. Solid (%): 45~70 o. Viscosity (cPs): 18,000 ~ 24,000 cPs (at 25ºC) o. Specific Gravity: 0.900 ~ 1.500 o. Flash point: 42~46ºC o. Boiling point: 165~220ºC
|
|
|
Outdoor Availability |
Weathering test of ink for high grade (color number 005 series) was carried out by CXWA Weather-o-meter, Accelerated Weathering Test Machine by ATLAS, U.S.A. (Norm Sunshine Carbon arc, 63±3ºC BP, 18 minutes/ 120 minutes Spray). Its weathering of all color ink proved to be excellent maintaining 5 grade of ISO Gray scale (1~5 grade) at 3,000hr, and this test result shows weathering can be guaranteed at least 3~5 years. To obtain more excellent weathering and light resistance, it is recommended to use our company’s “810 Medium Ink” for top coating.
|
|
|
Ink film test results |
|
Item |
Result |
Test Method |
Adhesion |
100/100 |
100 columns, Opp Tape, close contact |
Heat resistance |
Not affected |
80ºC x 10hrs, adhesion, gloss, no discoloration |
Water resistance |
Not affected |
50ºC x 24hrs, adhesion test after soaked in water for 1 hour |
Acid resistance |
Not affected |
Soaked for 2 hrs at 40% H₂SO₄ x 60ºC |
Gloss |
80 |
Average value after measuring 3 times at 60ºC |
|
|
※ Test Method 1) Used Ink : SG#4000 725 R. Black 2) Thinner/ Thinner Ratio : 5305 Thinner, Ink/Thinner = 100 / 20 3) Drying condition : Drying for 10 min at 60ºC, and air drying for 24 hours 4) Screen MESH : 305 per inch 5) Test materials : Untreated PP specimen 6) Adhesion Test : Scribe 100 pores by 1mm, stick OPP Tape, and apply instant power at 90º and rapidly remove it. Read the case of no splitting at printed film as 100/100. 7) Test of water resistance: Soaked in warm water for 24 hours at 50ºC leave it for 1 hour, then make an adhesion test. 8) Test of acid resistance : soaked in 40% H₂SO₄ solution at 60ºC for 2 hours, wash it out with clean water, leave it for 1 hour, and measure adhesion, color and gloss chance. 9) Gloss : Measure three printed parts at 60º gloss meter of BYK company and read average value.
Safety and Non-toxicity |
|
• It does not contain toxic substances such as carcinogen and heavy metal. • It does not contain heavy metal components such as Lead, Cadmium by the overseas standard. RoHS - Cd, Pb, Hg, Cr6+, PBBs, PBDEs • It has high natural ignition point, so it is safe if it is not intentional incendiarism. |
|
Caution |
|
• Fully stir up the contents prior to use that they can be mixed well. • Do not mix it with other kinds of ink. • It may not be fit with some materials, so use it after sufficiently looking it over. • Use a designated diluent by all means. • For products requiring light-resistance and heat resistance. Inquire them into the purchase shop. • Handle it at well-ventilated place, and keep it with its lid well closed at a designated place. • Keep out of reach of children. It is harmful by inhalation, in contact with skin and if swallowed. • Take notice of flames heats, and keep away from them. • For other inquiries, ask them to the purchase shop. “MSDS” is available on request |
|
|
|
|
|
|
PES Ink is silk screen ink for Polyester (PET - poly ethylene terephthalate) film material manufactured by mixing and istributing high class pigment s using polyester synthetic resin. PES inks forms excellent gloss and flexible film for its excellent adhesion and good workability.
|
|
Main features |
|
ITEM |
CONTENTS |
Ink type
|
Air-drying, Acrylic synthetic resin |
Applicable materials
|
Polyester (PET) film, PET stickers |
Gloss
|
High glossy (controllable to semi-gloss, non-gloss by matte agent) |
Drying time
|
Air drying 5~20 min / heat drying 10 min at 60℃ |
|
|
|
Specifications of Ink |
|
o. Appearance: Viscous fluid o. Solid (%): 45~70 o. Viscosity (cPs): 18,000 ~ 24,000 cPs (at 25ºC) o. Specific Gravity: 0.900 ~ 1.500 o. Flash point: 42~46ºC o. Boiling point: 165~220ºC |
|
|
Mixing Ratio of Hardener |
|
o. Used hardener : Poly hard UN-75 o. Mixing ratio : INK : hardener (5/1)=830g/170g o. Mix hardener with ink, fully then use it after 10 minutes. o. The ink with hardener mixed becomes hardened after 7~8 hours pass, so it needs to be mixed as the amount used to save cost. o. It takes 2~3 hours for drying of touch, and takes hardening hours (about 24 hours) for complete drying, so avoid the contact loading of printing materials within 24 hours. o. Adhesion test is required after 24 hours, the more time passes (2~3 days), the stronger the adhesive strength becomes. o. Keep it with its lid up well closed after using a hardener.
Safety and Non-toxicity |
|
• It does not contain toxic substances such as carcinogen and heavy metal. • It does not contain heavy metal components such as Lead, Cadmium by the overseas standard. RoHS - Cd, Pb, Hg, Cr6+, PBBs, PBDEs • It has high natural ignition point, so it is safe if it is not intentional incendiarism. |
|
Caution |
|
• Fully stir up the contents prior to use that they can be mixed well. • Do not mix it with other kinds of ink. • It may not be fit with some materials, so use it after sufficiently looking it over. • Use a designated diluent by all means. • For products requiring light-resistance and heat resistance. Inquire them into the purchase shop. • Handle it at well-ventilated place, and keep it with its lid well closed at a designated place. • Keep out of reach of children. It is harmful by inhalation, in contact with skin and if swallowed. • Take notice of flames heats, and keep away from them. • For other inquiries, ask them to the purchase shop. “MSDS” is available on request |
|
|
|
|
|
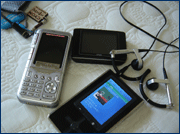 |
MIRROR-1000 is Baking type ink made by special synthetic resin and special metallic silver, which can generate a mirror effect on glass, PET, acrylic, and PMMA by the back printing on the transparent plastic film. Furthermore, the alternative effects include special metallic materials and hot stamping. Materials difficult for adhesion, such as undisposed PET (vacuum coating & hard coating), will necessitate the use of hardener. For glass, mirror 600 (one-component) and mirror 800 (two component) exist. For plastics, mirror 1000 (one-component) exist.
|
|
|
Main features
|
|
ITEM |
CONTENTS |
Ink type
|
Baking type denaturalized Acrylic Resin |
Applicable materials
|
PET, PC, Acrylic, PMMA
|
Gloss
|
High glossy, mirror effect
|
Drying time |
10 min. / 60°C
|
Thinner |
BC(Buthyl Cellusolve) |
Coverage Area and Packing
|
30~40 m²/kg Kg, 4kg, 17kg(Plastic can)
|
|
|
|
|
|
|
|
|
Specifications of Ink |
|
o. Appearance: Low viscous fluid o. Solid: 10% o. Viscosity: 900~1,000 cPs (at 25℃) o. Specific Gravity: 0.959~1.000 o. Flash point: 42~46℃ o. Boiling point: 165~220℃ |
|
|
Mixing Ratio of Hardener |
|
• Used hardener: K- hardener • Mixing ratio- INK : Hardener = 100: 3~7% • Mix hardener with ink, fully then use it after 10 minutes. The ink with hardener mixed becomes hardened after 7~8 hours, so it needs to be mixed as the amount used to save cost. • It takes 2~3 hours for drying of touch, and takes hardening hours(about 24 hours) for complete drying, so avoid the contact loading of printing materials within 24 hours. • Adhesion test is required after 24 hours, the more time passes (2~3 days), the stronger the adhesive strength becomes. • The rest of hardener must be used within a month and the hardener is sealed tightly not to contact with air. |
|
|
Safety and Non-toxicity |
• It does not contain toxic substances such as carcinogen and heavy metal. • It does not contain heavy metal components such as Lead, Cadmium by the overseas standard. RoHS - Cd, Pb, Hg, Cr6+, PBBs, PBDEs • It has high natural ignition point, so it is safe if it is not intentional incendiarism. |
|
Caution |
• Fully stir up the contents prior to use that they can be mixed well. • Do not mix it with other kinds of ink. • It may not be fit with some materials, so use it after sufficiently looking it over. • Use a designated diluent by all means. • For products requiring light-resistance and heat resistance. Inquire them into the purchase shop. • Handle it at well-ventilated place, and keep it with its lid well closed at a designated place. • Keep out of reach of children. It is harmful by inhalation, in contact with skin and if swallowed. • Take notice of flames heats, and keep away from them. • For other inquiries, ask them to the purchase shop. |
|
|
|
|
|
IMD Ink is two-component heat hardening ink consist ed of special synthetic resin. This requires flexibility and material of ink safe to high-temperature and high-pressure during formation; it is to adopt injection molding for various instrument boards, such as automobile , electric machine (washer, microwave, etc) which require great water resistance and durability.
The printing process is as follows : 1)printing the backside 2)over coating by binder 3)pre-forming 4)injection 5) product. Finally, its printed film is united with a forming resin by putting into mold.
|
|
Main features |
|
ITEM |
CONTENTS |
Ink type
|
Two component heat-hardening, special synthetic resin
|
Applicable materials
|
PC, ABS, PET
|
Gloss
|
Semi glossy (controllable to semi-gloss, non-gloss by matte agent)
|
Drying time
|
heat drying over 50min at 100~120℃ |
|
|
|
Mixing Ratio of Hardener |
|
o. Used hardener : Poly hard SL-450 o. Mixing ratio : INK : hardener=800g/200g o. Mix hardener with ink, fully then use it after 30 minutes. o. The ink with hardener mixed becomes hardened after 7~8 hours pass, so it needs to be mixed as the amount used to save cost. o. It takes 2~3 hours for drying of touch, and takes hardening hours (about 24 hours) for complete drying, so avoid the contact loading of printing materials within 24 hours. o. Adhesion test is required after 24 hours, the more time passes (2~3 days), the stronger the adhesive strength becomes. o. Keep it with its lid up well closed after using a hardener. |
|
|
Specifications of Ink |
|
o. Appearance: Viscous fluid o. Solid (%): 45~70 o. Viscosity (cPs): 17,000 ~ 20,000 cPs (at 25ºC) o. Specific Gravity: 0.900 ~ 1.500 o. Flash point: 42~46ºC o. Boiling point: 165~220ºC |
|
|
|
|
Insert binder needs another layer of adjacent binder on printing films, because the films and resins lead to a mixture of two different components. This binder must endure strong adhesion for its application to heat temperature.
|
|
Main features |
|
ITEM |
CONTENTS |
Ink type |
One-component Air-drying, Synthetic resin |
Applicable materials |
PC, PET, ABS, PS, AS |
Drying time |
heat drying 40 min at 120℃ |
Dilution solvent |
Standard solvent (10~20%) odorless solvent, 305, Kobel Slow dry solvent 306 Retarder 731 (0~10%) Washing standard solvent, 301,303
|
Mesh & emulsion |
폴리에스타 (PET 1000) 250~305/inch 나일론 (PA 1000) 250~305/inch 유제 : 디아조타입 (569), 이중경화타입 (LX, Proclaim, Poly+S) Polyester (PET 1000) 250~305/inch Nylon (PA 1000) 250~305/inch Emulsion : Diazo type (569), Dual cure type (LX, Proclaim, Poly+S) |
Coverage area & Packing unit
|
Printing area 30~40㎡ /kg, Steel can 1kg, 4kg(G/A), Plastic can 17kg |
|
|
|
|
|
|
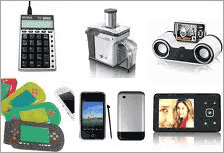 |
YD-U ink is an Urethane ink with two different types of components by hardeners, which is manufactured by mixing and distributing pigments using acrylic synthetic resin . It has excellent printing workability, adaptability to materials, adhesion, moisture resistance, and chemical resistance. YD-U ink is oriented to multi-purposes for heat-drying and air-drying as one of the most widely used inks among plastic materials that are difficult to attach and treat for heat intensity. Especially, K hardener among the two widely used hardeners, UL-60 and K, proves to be the most efficient one with 5% quantity. There are also excellent alternatives, such as ABS, ACRYLIC, and PC.
|
|
|
Main features |
|
ITEM |
CONTENTS |
Ink type
|
Air-drying / Two component heat-hardening, Urethane synthetic resin
|
Applicable materials
|
Plastic materials difficult to attach, multi-purpose acrylic, PC, ABS etc.
|
Gloss
|
Glossy (controllable to semi-gloss, non-gloss by matte agent)
|
Drying time
|
Air-drying, heat drying over 30min at 80℃
|
|
|
|
Mixing Ratio of Hardener |
|
o. Used hardener : ① Poly hard UL-60 ② Poly hard-k o. Mixing ratio : ①INK : hardener(4/1)=800g/200g ② hardener(5 %)=1000g/50g o. Mix hardener with ink, fully then use it after 10 minutes. o. The ink with hardener mixed becomes hardened after 7~8 hours pass, so it needs to be mixed as the amount used to save cost. o. It takes 2~3 hours for drying of touch, and takes hardening hours (about 24 hours) for complete drying, so avoid the contact loading of printing materials within 24 hours. o. Adhesion test is required after 24 hours, the more time passes (2~3 days), the stronger the adhesive strength becomes. o. Keep it with its lid up well closed after using a hardener. |
|
|
Specifications of Ink |
|
o. Appearance: Viscous fluid o. Solid (%): 45~70 o. Viscosity (cPs): 17,000 ~ 20,000 cPs (at 25ºC) o. Specific Gravity: 0.900 ~ 1.500 o. Flash point: 42~46ºC o. Boiling point: 165~220ºC |
|
|
|
|
|